THE FUTURE OF CARAVAN CONSTRUCTION
Throughout the decades, caravan manufacturers have experimented with numerous ways to build their vans. Some have stuck, some have been scrapped. There remains a handful of ways caravans are built in this country: aluminium sheeting over a meranti timber (dating back to 1940) or an aluminium frame; and one-piece composite aluminium or fibreglass panelling, also known as ‘sandwich panels’.
Some manufacturers have developed one-piece (monocoque) fibreglass shells, while others offer full plywood walls sheeted with aluminium. These, however, are the exception rather than the norm.
The trend, however, is towards one-piece composite aluminium or fibreglass panels. And for good reason. In this article, we’ll look at why this just might be the future of caravan construction in Australia.
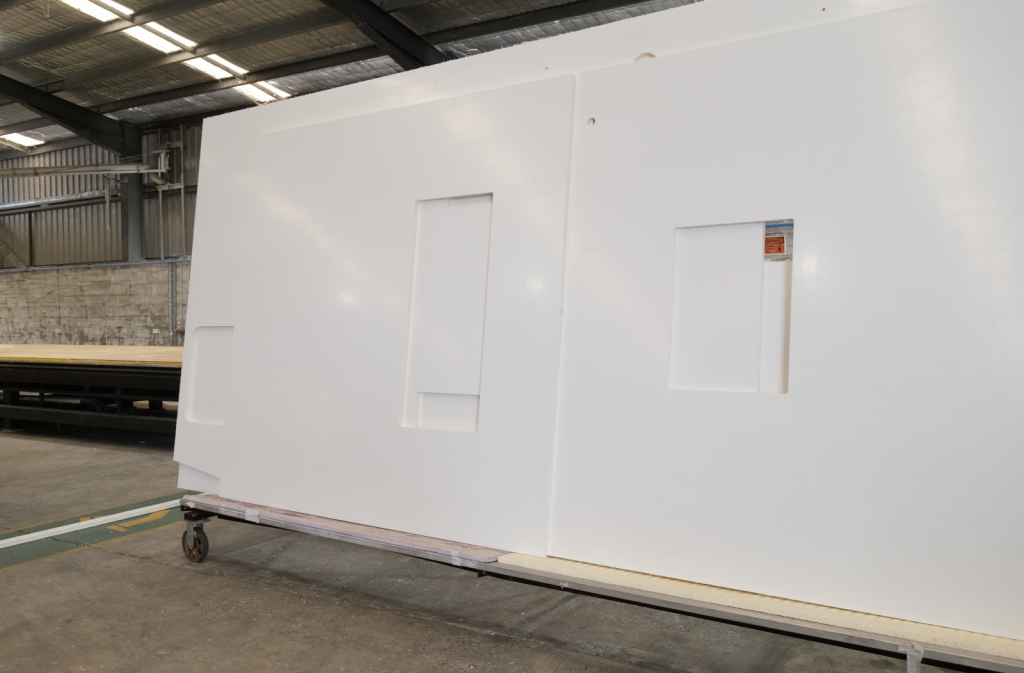
BENEFITS OF SANDWICH PANELS
What, precisely, do we mean when we say ‘one-piece’? Effectively, this refers to the fact that both side walls have no joins. They are a single panel spanning the length of the body of the van. The roof, meanwhile, is usually also a single panel, stretching from the drawbar to the very rear of the van.
Different manufacturers use different techniques to ‘lock’ these panels together, but ultimately there are fewer joins involved, which means the chances of the van springing a leak are greatly reduced.
During construction, when it comes to fitting things like windows and air-con units, the manufacturer will simply cut the correct shape out of the sandwich panel and secure the window or appliance without having to deal with framing, and seal it accordingly.
If a leak does occur, it should be much easier to repair because, in most cases, all you’ll need is a bead of silicone. Also, any water that does make its way inside can be dried out instead of being absorbed into any timber components and causing rot.
Sandwich panels get their name from the use of layers (hence the term ‘sandwich’).
Done right, they are relatively light while offering high mechanical strength and load-bearing structural properties. The lighter weight enables greater fuel efficiency, thereby reducing operating costs. This combination of lightweight construction and the excellent insulation makes sandwich panels an ideal choice for constructing truck bodies, semi-trailers, caravans and motorhomes.
Like a sandwich that you’d make for lunch, sandwich panels consist of two facings and a core. They are fabricated by attaching two thin, strong, stiff ‘skins’ (either fibreglass or aluminium) to a lightweight and relatively thick core between them.
The core usually consists of a lightweight foam, which provides the necessary structural integrity for the panel as well as insulation properties.
A composite sandwich panel offers particular mechanical advantages: the facings absorb traction and compression forces, while the core material resists shear and thrust forces.
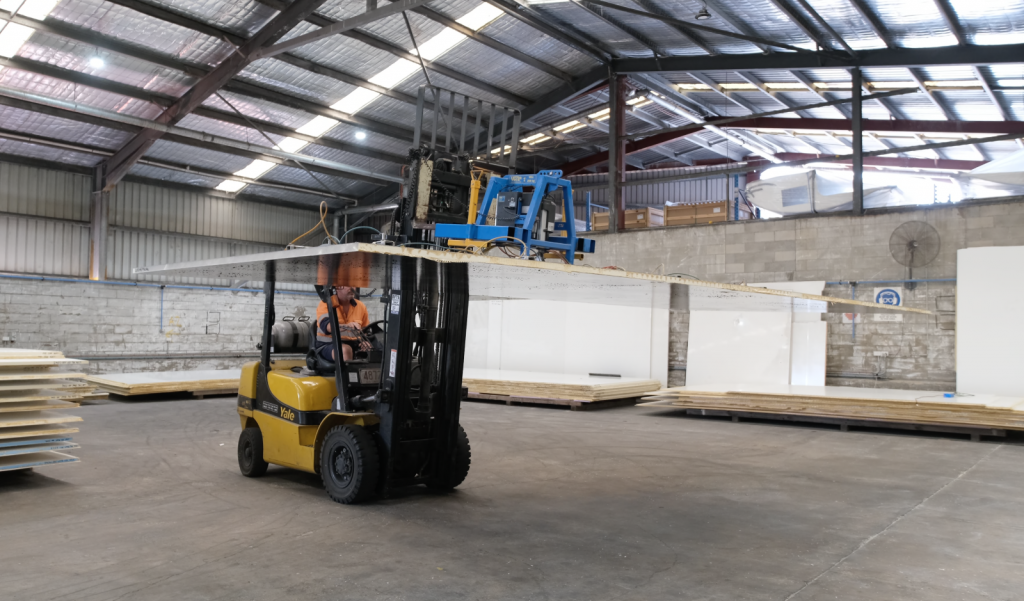
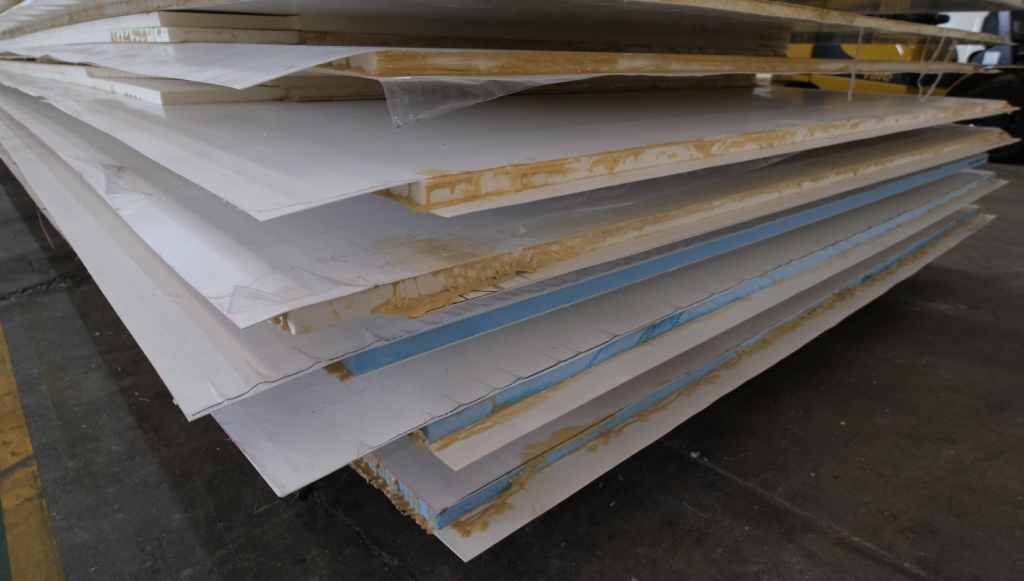
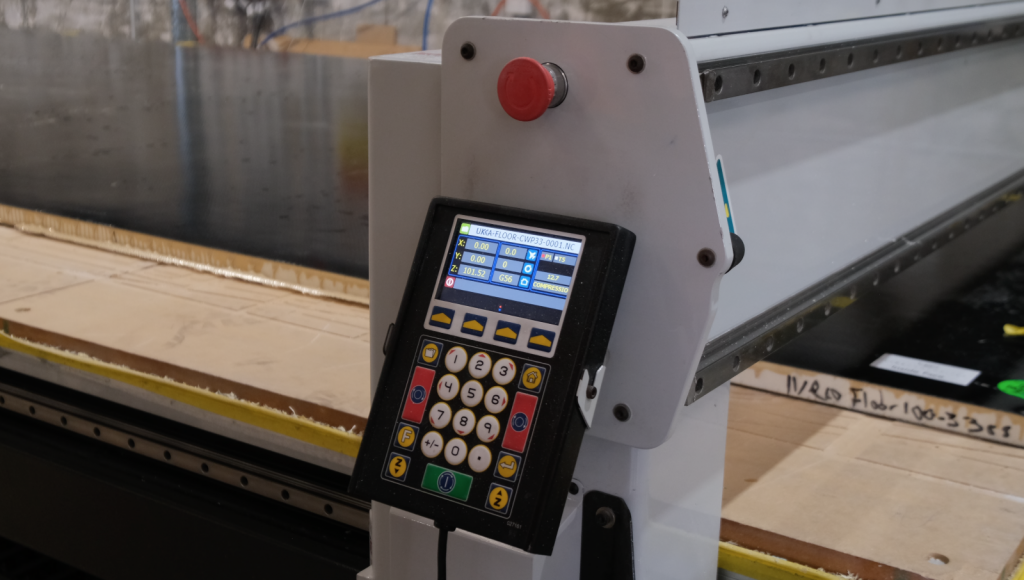
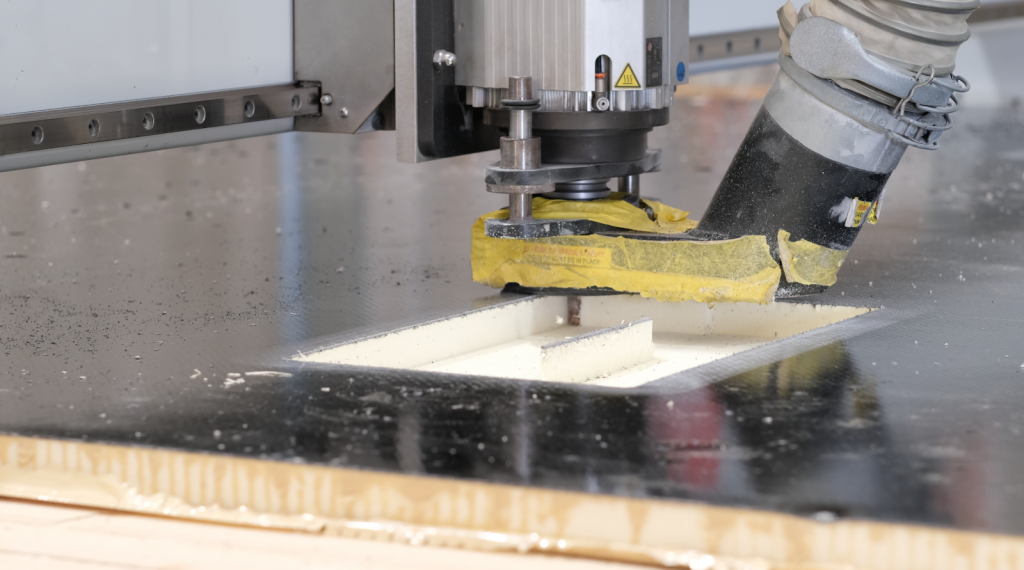
Each component of a sandwich panel plays a particular role:
FACES: The faces carry the tensile and compressive stresses in the sandwich. Local flexural rigidity is so small it can often be ignored.
CORE: The core’s function is to support the thin skins so that they do not buckle, and to keep them in relative position to each other. To accomplish this, the core must have several important characteristics. It has to be stiff enough to keep the distance between the faces constant. It must also be so rigid in shear strength that the faces do not ‘slide over each other’. The shear rigidity forces the faces to ‘cooperate’ with each other. If the core is weak in shear strength, the faces will not cooperate and the sandwich will lose its stiffness.
It is the sandwich structure as a whole that makes this type of panel so beneficial. However, the core has to fulfil the most complex demands. Strength in different directions is not the only property that the core has to have. Often there are special demands for buckling, insulation, absorption of moisture, resistance to ageing, etc.
ADHESIVE (bonding layer): To keep the faces and the core cooperating with each other, the adhesive between the faces and the core must be able to withstand and transfer the shear forces between them. The adhesive must be able to carry both shear and tensile stresses.
It is hard to specify what kind of demands an adhesive needs to meet. A simple rule is that the adhesive should be able to withstand the same shear stress as the core.
SIMILAR TO I-BEAMS: Sandwich panels are comparable to an endless I-beam in the sense that when subjected to bending, the flanges carry in-plane compression and tension loads while the web carries shear loads.
In a sandwich panel, the sandwich skins or laminates are like the flanges while the core is like the web.
Like an I-beam, when the skins are further apart, the structure gains more proportional stiffness.
A thicker core achieves the same, but it also provides an overall low density, resulting in a high stiffness-to-weight ratio.
One of the big differences between designs with conventional materials and a sandwich composite solution is the small weight penalty for increased thickness.
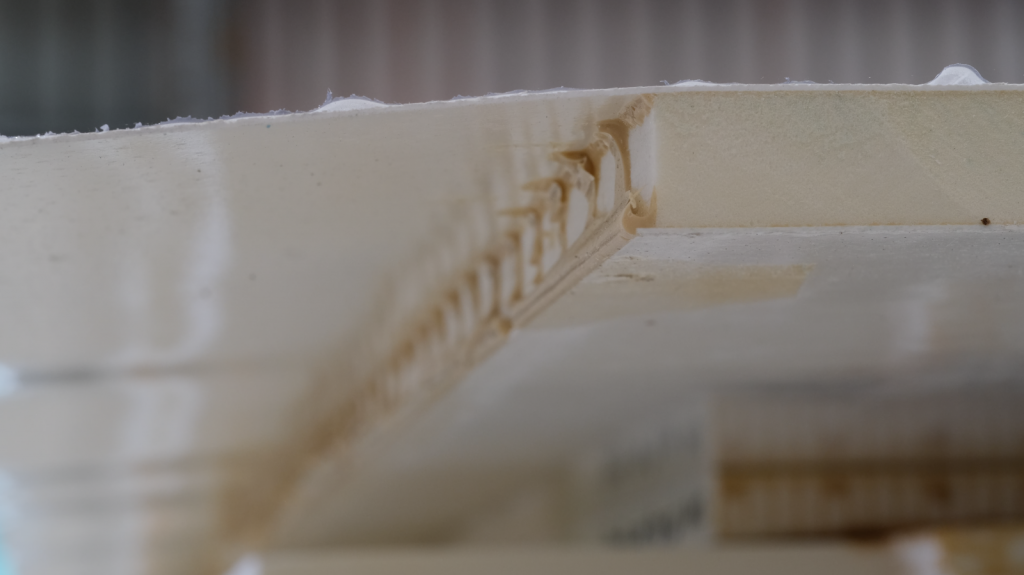
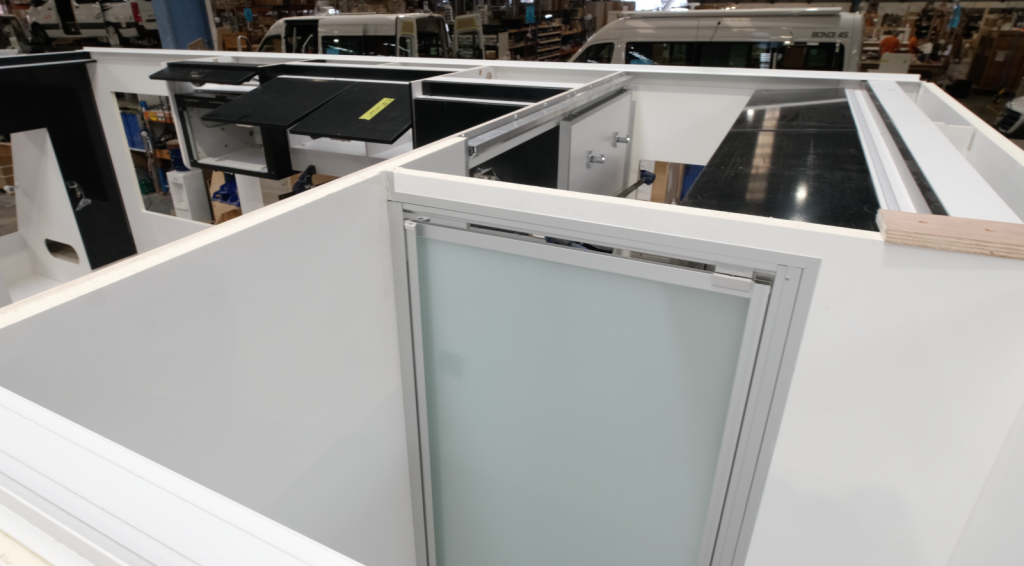
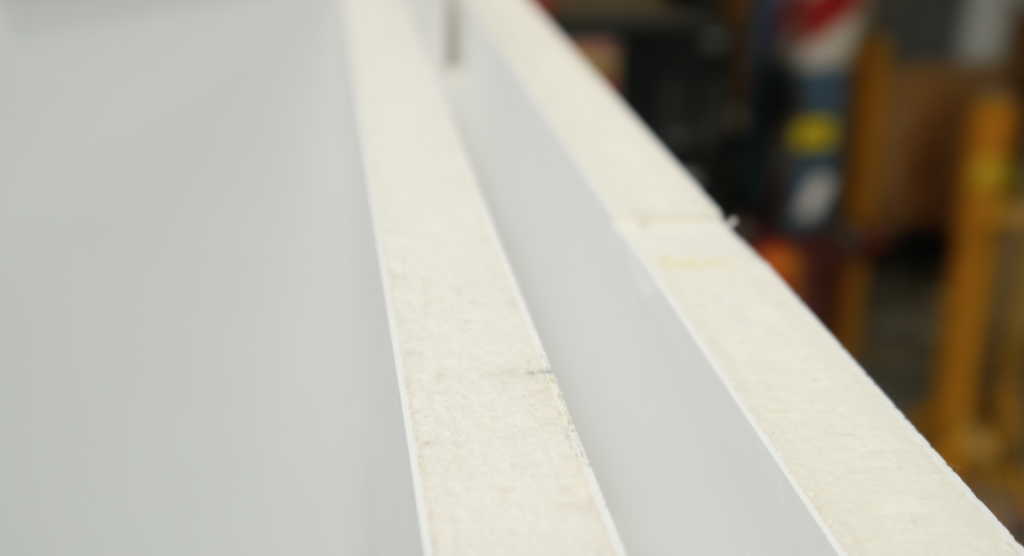
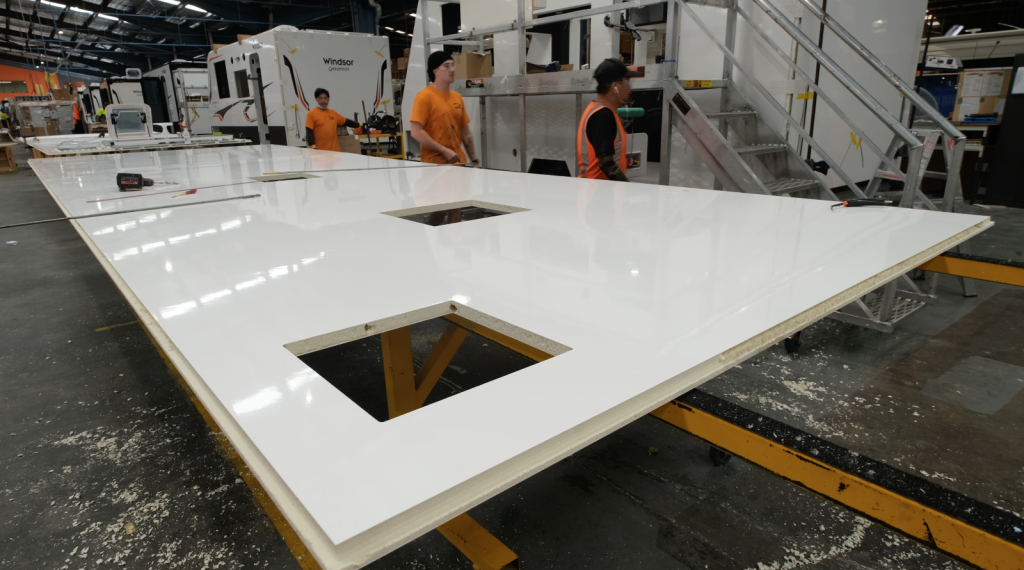
WHY WE WENT COMPOSITE
We asked Marty Ledwich, who has spent years travelling around Australia full time with his wife, for his opinion on composite sandwich panel construction…
After owning a van with a wooden frame and another with an aluminium frame, we have chosen to build our next van using a full composite construction.
There are several reasons for this. First, because there is no internal frame, there is a significant weight advantage with composite construction over more traditional methods. And just because there is no frame doesn’t mean the van will be less rigid.
In fact, a properly constructed composite van will actually be more rigid than a framed van. This is due largely to the way the individual walls and roof are bonded together as large single pieces rather than lots of small bits nailed, screwed and glued together.
The lack of joins results in a very flat, clean surface on which all the external features such as windows and hatches can be fixed to. This aids sealing and greatly reduces the risk of water ingress.
While all these advantages are fantastic in their own right, two major considerations sold us on composite construction. It offers significantly better insulation against extreme hot and cold weather. When travelling this country year-round, as we do, you encounter weather extremes very often. Air-conditioners and internal heaters work much more efficiently. Composite vans are just nicer to live in regardless of what’s happening outside.
Finally, composite vans last much longer than aluminium-clad vans. They are less prone to damage from slight knocks and bumps, and particularly from hail. In fact, this durability and long life often results in lower insurance premiums.
As an example, CIL Insurance offers composite van owners a 10 per cent discount premium for caravans with full composite walls and fibreglass exterior cladding. That sort of confidence was enough to convince us of our decision.
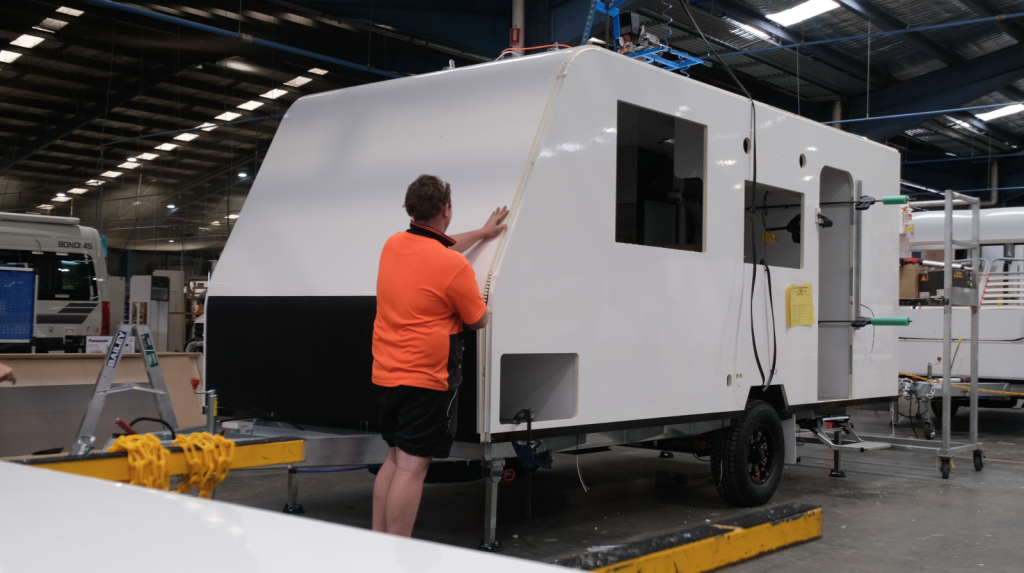
HISTORY
Composite panels, especially fibreglass, for caravans have their roots in Europe, where the emphasis is on lightweight caravanning. The benefits eventually became clear to Australian manufacturers.
The sandwich panel technique came into wide use during the 20th century, largely in response to the demands of the aerospace industry to optimise strength-to-weight ratios.
Today, automated methods of production and a much larger selection of facing materials, cores and adhesives have permitted the production of composite sandwich panels that can be tailored to meet a vast range of requirements in diverse fields of application.
It’s been long understood that two materials with a lighter material in between them increases the stiffness and strength of a structure while keeping weight and costs low.
It also allows for greater freedom of design. In transportation, lower weight enables higher payloads.
Rising fuel costs and increasing awareness about the importance of environmentally-friendly solutions has meant innovative construction methods like sandwich panels are becoming more popular for structural design.
Every kilo saved in the construction of any vehicle, whether a truck, semi-trailer, caravan or motorhome, results in less energy needed over its lifetime.
The sandwich design is a great way of reducing weight while having a high strength-to-weight ratio and energy absorption abilities.
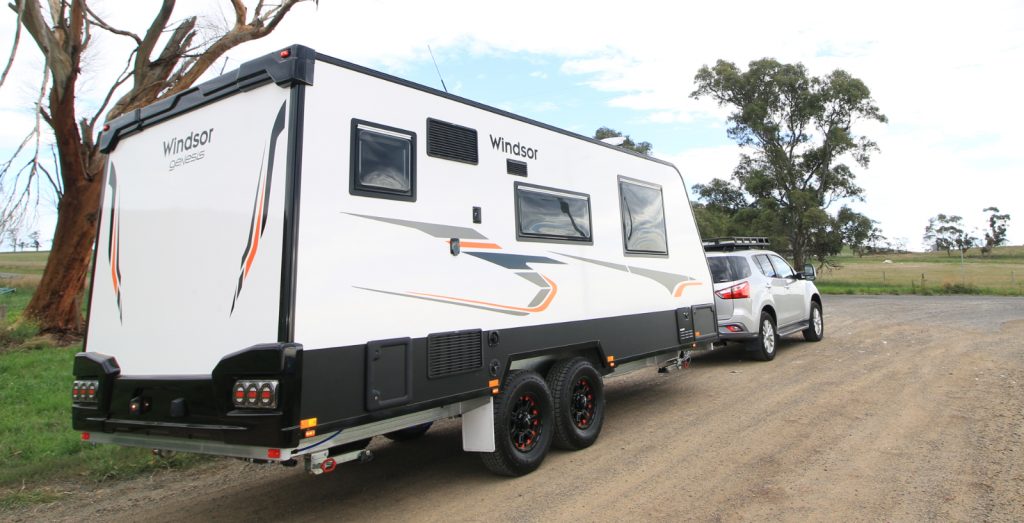
HOUSE OF WINDSOR
Manufactured by Apollo RV in Queensland, all Windsor caravans are nowadays built using composite construction methods. We asked Windsor for an insight into how this company builds its panels…
Windsor Caravans’ panels are fabricated by attaching two strong, stiff fibreglass panel skins to a lightweight, thick foam core. The parts are bonded with a special glue (to ensure mechanical strength) and vacuum pressed.
Windsor lays the sandwich panels into a big CNC machine to cut them to shape, including routing out spaces for windows, entry doors, the rooftop air-conditioner, roof hatches, etc. According to Windsor, the precision of its CNC machine ensure a tolerance of one millimetre, which helps the assembly of windows and components, and ensures the best seal possible.
Windsor said that the use of composite panels made their designs “even more advantageous as they offer at least the same or even higher levels of strength as aluminium alloy or steel but with a greater level of stiffness”.
“Positive aspects of fibreglass sandwich panel construction are: durability; they are lightweight and thermally efficient; they are dimensionally stable and moisture resistant; and they are completely recyclable and easy for a specialist to work with in case there is a need of repair,” Windsor told GoRV.
Thanks to Windsor Caravans for its assistance with this article. Windsor is a great choice when it comes to composite RVs. These vans are designed and built in in the company’s Brisbane factory. If you’re in the market for a van and composite construction sounds like the way to go, why not put Windsor on your shopping list?
The post THE FUTURE OF CARAVAN CONSTRUCTION appeared first on GoRV.
Source: https://www.gorv.com.au/the-future-of-caravan-construction/